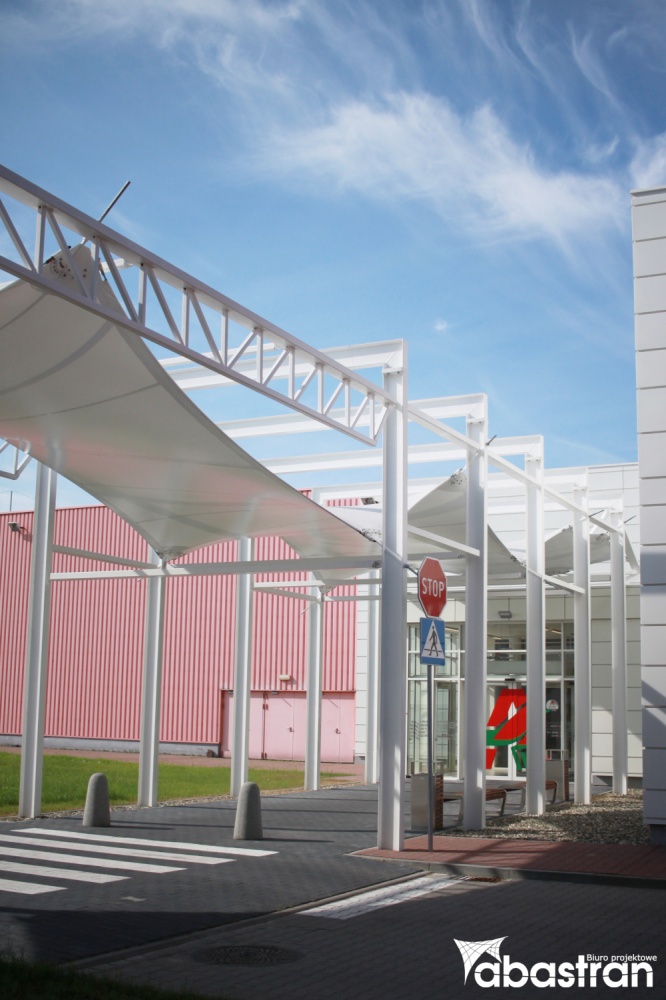
Key Stages in Steel Structure Design
In recent years, we have observed a dynamic increase in demand for advanced steel structures, clearly indicating the growing importance of this sector in modern construction. Designing steel structures is a complex process that requires not only engineering knowledge but also the ability to combine technical aspects with economic ones. This is particularly evident in the implementation of specialized projects, such as membrane structures, ETFE, or tent structures, where the traditional design approach must be modified.
The key to success in designing steel structures is an integrated approach that considers not only the conceptual phase but also production and assembly aspects. Experience from complex projects, like large-span roofs or inflatable halls, shows that early collaboration between designers and the production and assembly departments helps avoid costly mistakes and optimizes the entire investment process. In this article, we will present a comprehensive approach to designing steel structures, based on many years of practical experience and the latest technological trends.
Stages of the Steel Structure Design Process
Professional steel structure design is a multi-stage process that requires a systematic approach and in-depth knowledge of both technical and formal aspects. Regardless of the type of structure – whether we are talking about classic steel halls or specialized membrane structures – the design process can be divided into five key stages that determine the final success of the project.
First Stage – Requirements Analysis and Concept Development
The first stage is requirements analysis and concept development. At this stage, we gather information regarding the intended use of the facility, site conditions, investor expectations, and budget constraints. It is also crucial to identify ground conditions, climatic conditions, and environmental loads that will affect the structure. According to Eurocode 3 standards (PN-EN 1993), we determine the consequence class of the structure and the associated reliability requirements at this stage. We often encounter situations where insufficient initial assessment leads to costly changes in later project phases, which is why a thorough analysis of all factors is so important.
Second Stage – Modeling and Structural Analysis
The second stage is modeling and structural analysis. Using specialized engineering software, we create a computational model of the structure, considering all significant load-bearing elements and connections between them. Then, we perform static and dynamic analysis, verifying the structure’s behavior under various load combinations according to PN-EN 1990 and PN-EN 1991 standards. For special structures, like membrane roofs or inflatable halls, advanced non-linear analyses considering the specifics of materials and geometry are necessary. Remember, verifying the computational model is crucial at this stage – even the most accurate calculations cannot compensate for errors in the initial assumptions.
Third Stage – Dimensioning of Structural Elements
The third stage is the dimensioning of structural elements and connections. Based on the analysis results, we select appropriate cross-sections for steel elements and design the connections between them. This process must comply with the requirements of Eurocode 3, considering ultimate limit states. We pay special attention to connections, which are often the weakest links in the structure. In our design practice, we apply the 30/70 rule – allocating 30% of the time to concept and analysis, and 70% to optimization and detailed dimensioning of elements and connections. This approach helps us avoid many problems during the execution phase.
Fourth Stage – Development of Execution Documentation
The fourth stage is the development of execution documentation. At this stage, we create detailed workshop drawings, material specifications, and assembly instructions. The documentation must comply with the requirements of the EN 1090 standard, which specifies the execution classes for steel structures. For special structures, like tent hall covers or flexible tanks, the execution documentation must consider the specifics of the production technology, e.g., the requirements for PVC welding. From our experience, it is always worthwhile to verify design assumptions against production capabilities already at the concept stage, which helps avoid situations where designed elements are impossible to manufacture.
Fifth Stage – Author’s Supervision and Cooperation with the Contractor
The final, fifth stage is author’s supervision and cooperation with the contractor. Even the best-prepared documentation requires interpretation and adaptation to site conditions. As designers, we actively participate in the implementation process, solving emerging problems on the fly and verifying compliance of the execution with the design. In the case of non-standard structures, our presence during key assembly stages is absolutely essential to ensure the safety and functionality of the structure.
Optimization of Steel Structures
Optimization of steel structures is a process that goes far beyond simply saving material. The modern approach to optimization considers the entire life cycle of the structure – from material and production costs, through assembly time and ease, to operation and potential dismantling. Especially in the case of specialized structures, it becomes a key element of the design process.
Reducing the structure’s weight is a classic aspect of optimization that directly impacts material and transport costs. Modern topology optimization methods allow us to identify and eliminate unnecessary material while maintaining the required load-bearing capacity and stiffness of the structure. In our design practice, we use sensitivity analysis to changes in material parameters, which helps determine which structural elements are crucial for its safety and which can be optimized.
Selecting steel cross-sections is a process that should consider not only strength requirements but also technological and economic aspects. Using standard profiles, available without special ordering, can significantly reduce costs and lead time. On the other hand, for structures with high aesthetic or functional requirements, it is worth considering the use of special profiles, which can provide better properties with less weight. The selection of cross-sections should also take into account production technology – some profiles may be easier to process or weld, resulting in lower manufacturing costs.
Connection optimization is an often overlooked, yet extremely important aspect of steel structure design. Different connection solutions (welded, bolted, riveted) have different costs, time requirements, and quality control demands. In temporary structures, like stage roofs or advertising tents, we use detachable connections that allow for quick assembly and disassembly. Conversely, in permanent structures, like industrial halls or tanks, welded connections can provide better tightness and durability.
Summary
Steel structure design is a dynamically developing field, combining traditional engineering knowledge with modern technologies and optimization methods. A comprehensive approach, considering the entire life cycle of the structure – from concept, through production and assembly, to operation – allows for the creation of facilities that combine functionality, safety, and economic efficiency. Especially in the case of specialized structures, like roofs or ETFE structures, the integration of different areas of knowledge and experience is key to success.
At Abastran, we specialize in the design and implementation of advanced structures. Our many years of experience in structural optimization allow us to deliver solutions that are not only safe and functional but also economically justified. Thanks to close cooperation between the design and production departments, we are able to execute even the most demanding projects while maintaining the highest quality standards.
If you are planning a project requiring advanced structural solutions, contact us. Our team of experienced designers will help you find the optimal solution tailored to your needs and capabilities.
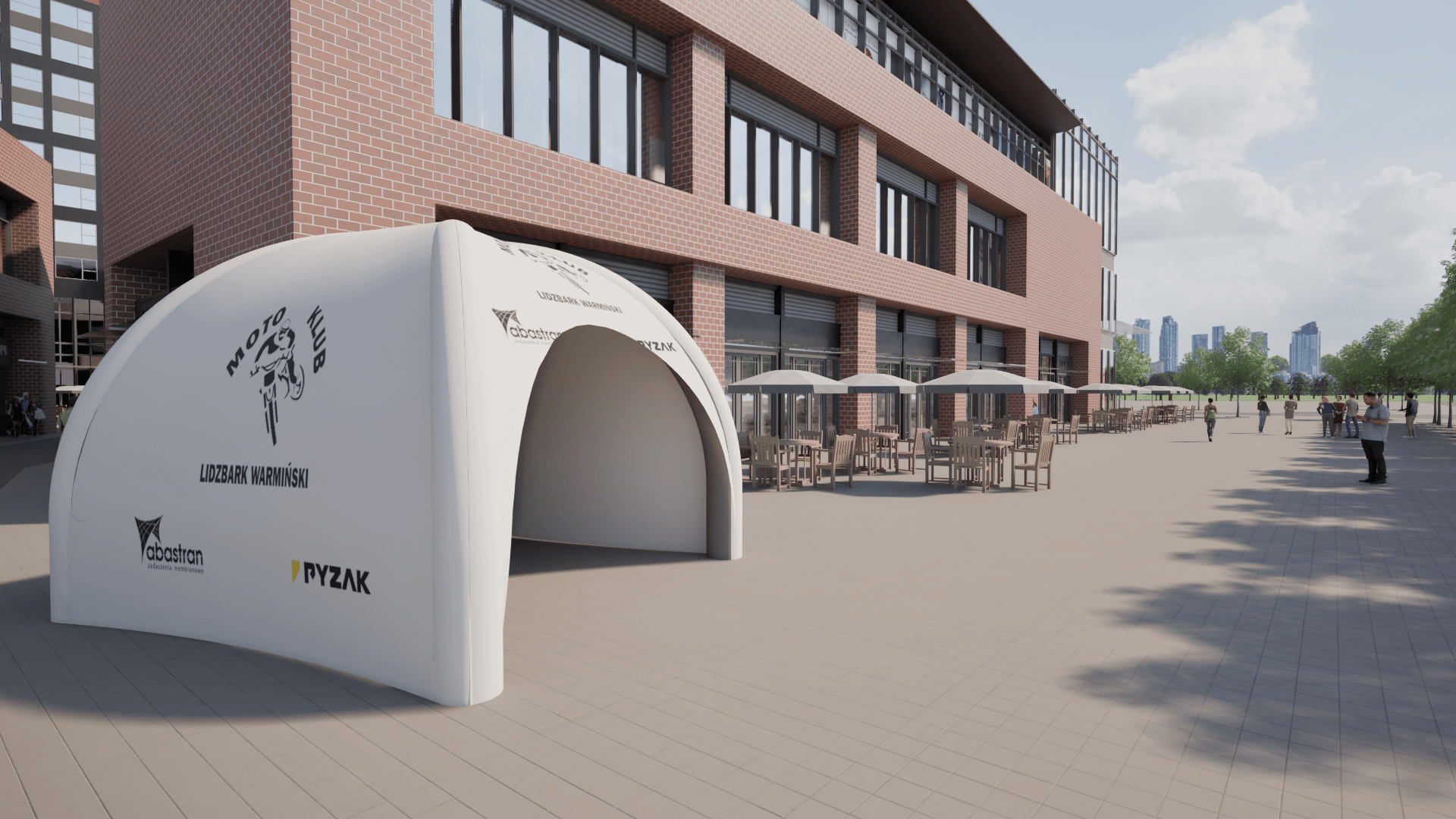
Advertising Tents as an Investment – How to Increase Brand Recognition at Events?
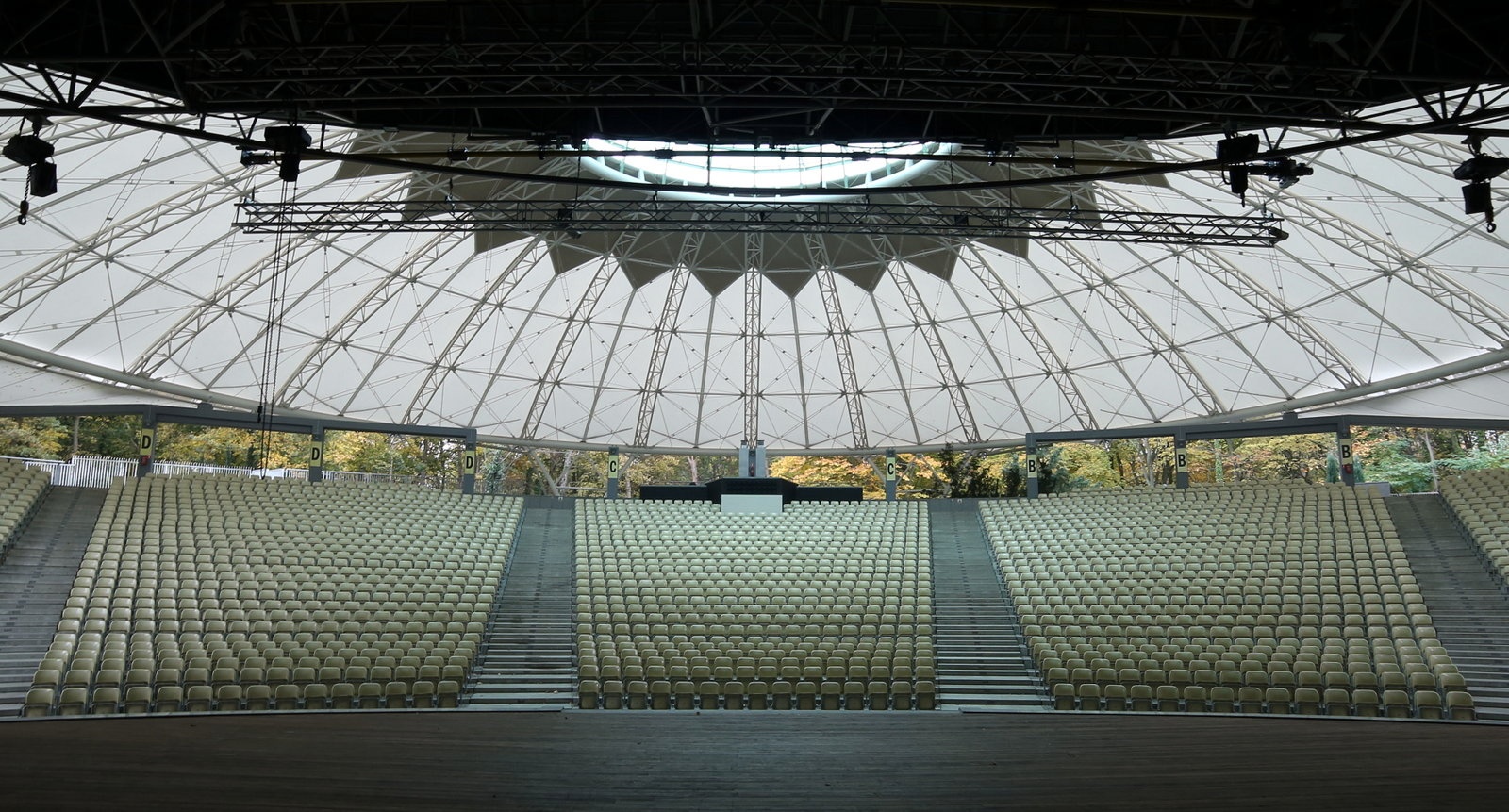

Competition for Innovative Membrane Roofing – Results and Inspirations
This year, we had the pleasure of organizing a competition together with the Faculty of Architecture at the Silesian University of Technology for 6th-semester students to design innovative membrane roofing. The award ceremony, held at the Faculty of Architecture in Gliwice, was the culmination of the young designers’ creative and technical journey.